This (more) travel-sized ukulele project has been tremendously satisfying! The woodworking part filled me with unbounded joy, and hopefully the music part will be fun, too. The main ‘feature’ of this ukulele is that the tuning pegs (I chose geared ones since they are easier to tune, and I will need all the help I can get) are mounted in the body. This way, the head isn’t needed, making the uke a bit shorter. However, it does make the body unconventional, and probably messes with the acoustics (which I don’t really understand anyway). This is going to be a long blog post – get ready!
As some of you know, I procured a chainsaw a few weeks ago. Its electric, so its not quite as powerful as a gas saw, but still way more going on than me behind a hand saw. Around that time, the walnut tree growing in the front yard was trimmed, special attention to the dead looking branches that overhung the roof. Naturally I was attracted to the stuff that was cut off, and I proceeded to saw some of it up to see if I could help it dry faster and more evenly. I know you can paint stuff on the end to really help control how wood cures and prevent cracking. I didn’t do that. Laziness.

The pieces that had been dead for a while looked almost ready to work. So after waiting a few weeks (and after sharpening my jointer knives) I ran the first piece over the jointer and was not disappointed.

The first thing I wanted to cut was the book matched pieces for the front sound board. I think the spindle on the table saw wobbles slightly and not everything is square, so the cuts didn’t come out that smooth. Also, the saw kerf is pretty wide and the log diameter is pretty small, so the book match pattern isn’t perfect – pretty satisfactory for my first stab at a book match though!


Next I turned my attention to the neck. I ripped and thickness sanded a wide strip of maple to be sandwiched between two thicker pieces of walnut.

The result is a bright white line, that I think provides an attractive contrast to the walnut.

Since the wood had been dead for a while, some of it had some insect damage. I was really careful with how I arranged my neck sandwich with the hope that the insect hole areas would eventually be cut away.

While the glue for the neck was drying, I cut the pieces for the body. Because I wanted to mount the tuning pegs on the body, I knew the body sides would have to be quite thick.




Now back to the neck. I forgot to take photos of the tenon being cut with my tenoning jig, but that happened (you can see part of it on the end of the neck facing away from the camera in the photo below).


With the profile of the neck roughly shaped, I glued on a thin piece of cocobolo which will later serve as a visual accent for the end of the neck, and also provide a small thickness increase at the very end of the neck, which I find to be a pleasant thumb detent.

Finally we commence some truly satisfying woodworking when the whittling begins. Some of you may recognize this knife from a previous build.

After getting the rough shape with a knife, I smoothed things out a bit with a fine rasp.

To compliment the cocobolo accent at the top of the neck, I added one on the heel. I roughly cut it to shape before gluing it on.



While the heel cap glue drying, I glued some blocks into the body to form the slot that the neck tenon will glue into. I’m assuming the glue will be enough to hold the string tension on this particular uke. The piece of plywood in the middle is cut and shimmed to be the same width as the tenon.

And because I was pretty sloppy with gluing in those blocks, I trimmed the body again with the table saw.

The tenon cut wasn’t perfect, so I very patiently sanded the shoulders a little, using the uke body as a guide.
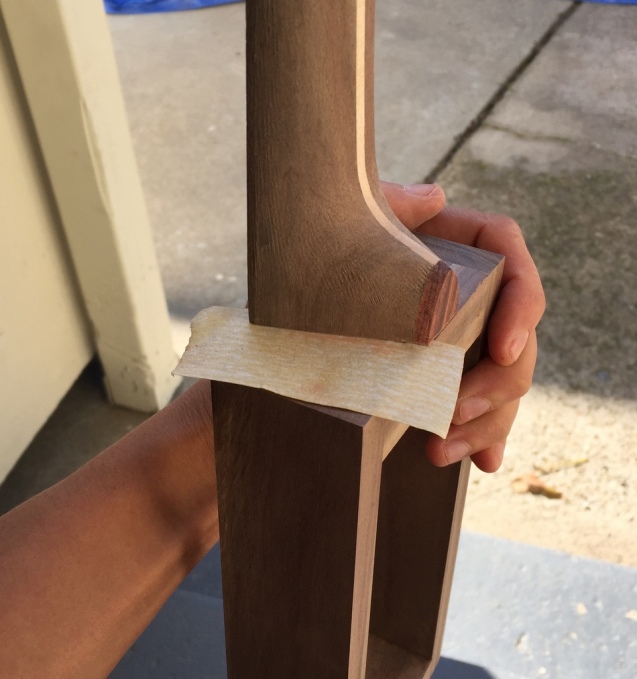
About this time I made a little test block to see how the tuning pegs would fit into the sides. I think the pegs I picked were too short… To compensate, I thinned the sides of the body (shown below is after thinning, the block I am holding is the original thickness).

In order to have tuning pegs in the body, the strings have to wrap around the end of the body and route into the body. To reduce friction, I made a smooth mandrel for the strings to wrap around. I started by rounding over a piece of cocobolo on the router.

Next I put some scallops on the end for decoration using my roommate’s mill. I guess I could have carved this, but the mill was right there…

Around this time, the test fits got really exciting!! You can see the more or less finished mandrel on the right. Next to it is a ready-made rosewood fretboard that I bought off eBay. They don’t have the greatest fit and finish (some of the edges on this one are too heavily chamfered), but for the most part, they are okay. $7 seems like a good tradeoff to avoid lots of tedious measuring and sawing (at least for my first stab at this luthier thing).

Next I laid out and drilled the holes for the tuning pegs. I was careful to back the hole with some sacrificial material during drilling to minimize tear out.

To provide clearance for the tuning pegs to turn, I needed to scoop out some material on the sides. I knew I’d end up hand carving part of it, but I removed a lot of material with a forstner bit first.



Shortly after sanding the tuning peg scoops, I cut the sound board to size (a little big actually), and glued it to the rest of the body assembly.
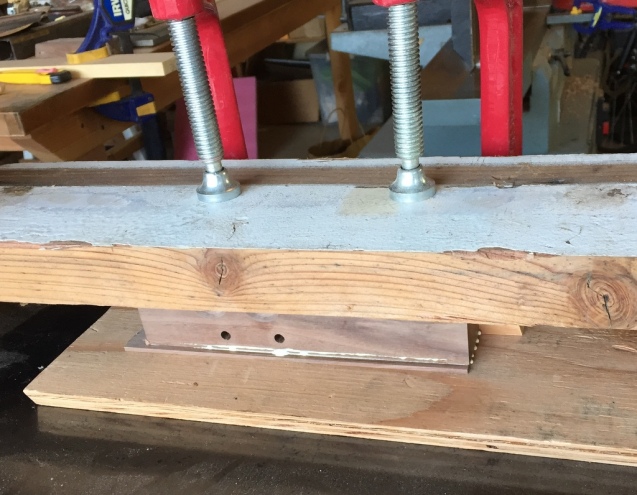
While that dried, I again turned my attention to the neck assembly. Turns out the walnut wasn’t totally dry. After a few days, there was a slight bit of unevenness in the fretboard gluing surface, so I sanded it down. Fingers crossed that the extra moisture is pretty minimal and doesn’t cause any problems in the long run…

About this time I realized that I had forgotten to cut the nut slot while the sides of the neck were still square. Oops. So I set the miter jig on the table saw using the neck itself as a guide.

A test piece showed this actually works out pretty well, so here goes the real thing!



Next I glued the neck to the fretboard so that I will be able to sand the edges of the fretboard perfectly flush with the edges of the neck.

Again as the neck dried, I turned my attention back to the body and trimmed the edges flush.

While planing the edges, I got a little sloppy and took out a pretty big chunk.

To fill the unsightly nick, I found an appropriately sized wood chip and used a generous amount of glue. The resulting fix is surprisingly good. I think most people won’t find it unless they are looking for it.

After sanding the edges of the neck flush to the fretboard, the width of the neck had naturally decreased – so much so that the neck now felt too thick, so I shaved away some more material and sanded smooth again.







Part way through the project, I decided I wanted a removable back cover. This would allow me to still access the tuning pegs when I needed to, but hide them for the most part. I think it might also make it a bit louder?? I don’t know, I honestly can’t tell.

Its crazy how many clamps are needed to glue something so small. I intentionally made the frame larger so that I could carefully sand down and ensure a tight fit with the ukulele body.

I used what was left of my book match from the soundboard to do the back as well.


Finally, I started filing notches for the strings and tuning the height of the bridge so that the string would the the right distance from the frets. It took quite a bit of iteration and time, but I knew it would be bad to overshoot it.

Finally, after lots and lots of sanding, I was ready for finish. I opted for several layers of Tru-oil (similar to Tung Oil) for its simplicity in application and the naturalness of the feel.








It’ll take me forever to learn how to play this, but at some point a video will be posted. Stay tuned…
**May 28, 2017 – finally wrote about the updates that I made on this uke to make tuning easier**
Leave a Reply
You must be logged in to post a comment.